The Time We Almost Lost a Shipment and What We Learned
It was supposed to be a routine shipment. But when our team checked the tracking system, the package had vanished—rerouted to the wrong country with no way to retrieve it in time. What happened next was a race against the clock to save our client’s deadline and avoid a costly disaster.
At TradeLink Solution, we’ve handled thousands of shipments across the globe, navigating tight deadlines and last-minute changes. But this particular shipment tested our ability to adapt under pressure. In the end, we managed to turn a potential disaster into a valuable lesson—and a better logistics strategy.
The Shipment That Almost Didn’t Make It
One of our key clients had an urgent order: a high-value shipment of specialized electronic components that needed to reach a factory overseas within 48 hours. These weren’t just any parts—they were custom-made for a medical device manufacturer. A delay would mean production shutdowns and financial losses in the tens of thousands of dollars. The client was already on edge, and failure was not an option.
Everything seemed to be running smoothly. The documents were in order, logistics partners were lined up, and tracking showed the shipment moving as planned.
But then, something went wrong.
As the package was being transferred at a major international hub, a miscommunication between two carriers caused it to be rerouted incorrectly. Instead of heading to its intended destination, it was mistakenly sent to a secondary processing facility in the wrong country—one notorious for customs backlogs and slow processing.
By the time we noticed, precious hours had already been lost. If we didn’t act fast, our client’s production line would grind to a halt.
The Race Against the Clock
The first challenge was pinpointing exactly where the shipment had gone. Our tracking system helped us locate it quickly, but just knowing where it was wouldn’t be enough—it was stuck in a logistics black hole, with no automatic way to reroute it.
At that moment, the entire team sprang into action:
- Our operations manager contacted both the airline and the facility’s logistics team to request urgent intervention. Normally, requests like these follow a bureaucratic process that takes days, but in logistics, relationships matter. Because we had worked with these partners before, we were able to escalate the request and get a response within the hour.
- The biggest issue? Cargo slots on direct flights were full. Instead of waiting for an opening, we got creative. We arranged for the package to be sent on a faster regional route to a nearby airport, where another carrier could pick it up and complete the final leg.
- We updated the client in real time, ensuring transparency and keeping their production team prepared.
It wasn’t a perfect solution, but it shaved off crucial hours and ensured the shipment arrived on time.
Lessons Learned from the Close Call
This experience reinforced several key lessons that have since strengthened our approach to logistics:
✅ Real-Time Tracking Needs Human Oversight
Automated tracking is essential, but nothing replaces an attentive logistics team that actively monitors high-priority shipments. If we had waited for an automated alert, we might have missed the chance to intervene.
✅ Strong Industry Relationships Can Save the Day
Because we had built strong partnerships with carriers and logistics hubs, we were able to get immediate assistance. If we had been just another company calling for help, we likely would have been put in the standard queue.
✅ A Plan B (and C) Should Always Be in Place
Logistics is unpredictable. Having alternative routes and contingency plans ready ensures that unexpected problems don’t turn into disasters.
✅ Clear Communication Prevents Costly Mistakes
This entire situation started because of a simple miscommunication between two carriers. Since then, we’ve implemented stricter coordination processes to reduce the risk of similar mistakes.
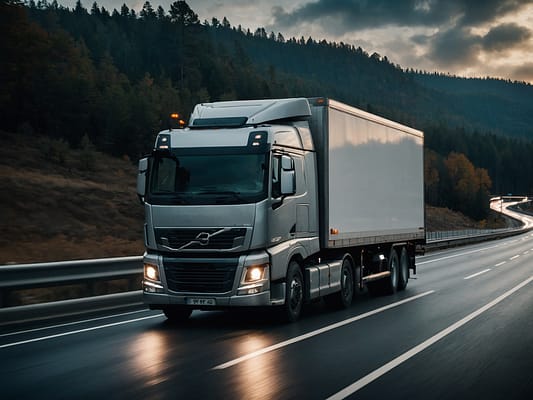
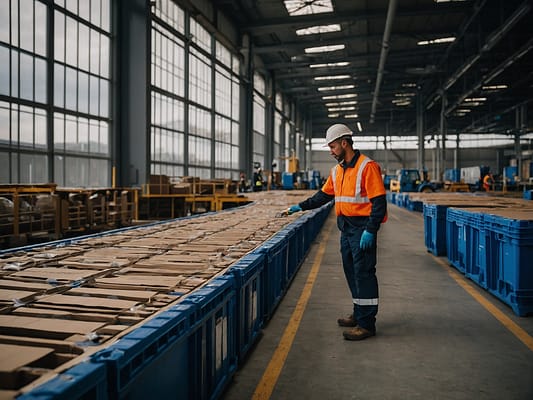
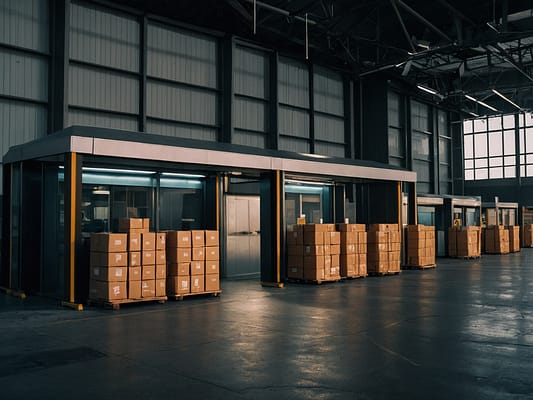
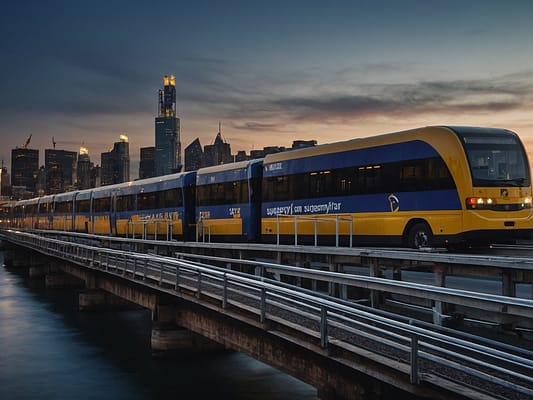
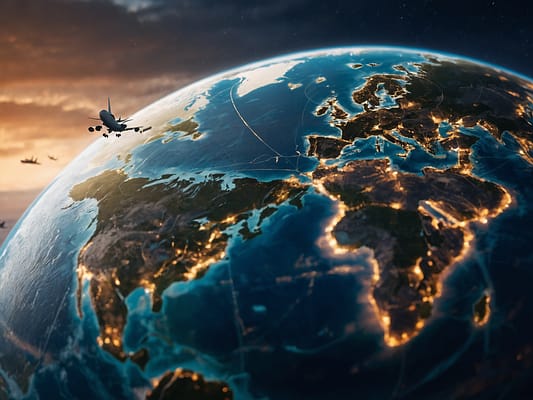
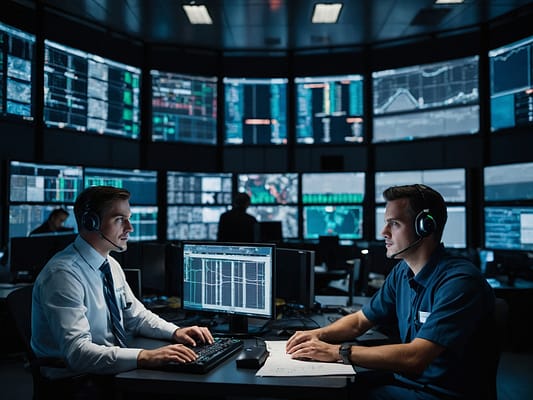
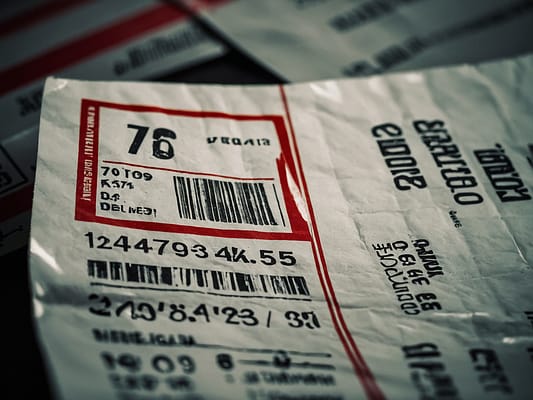
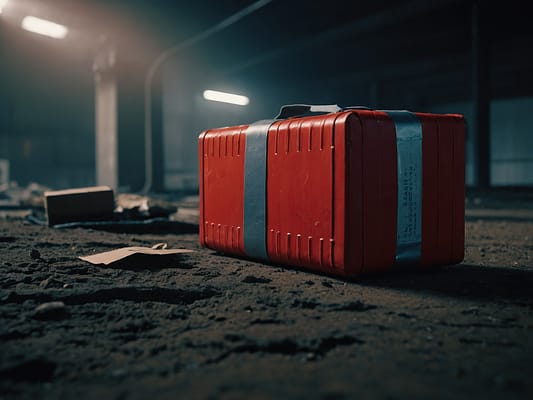
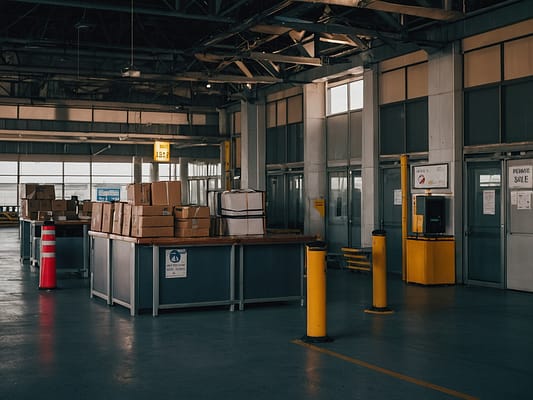
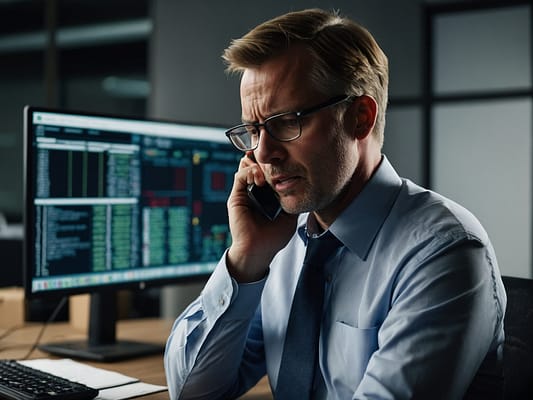
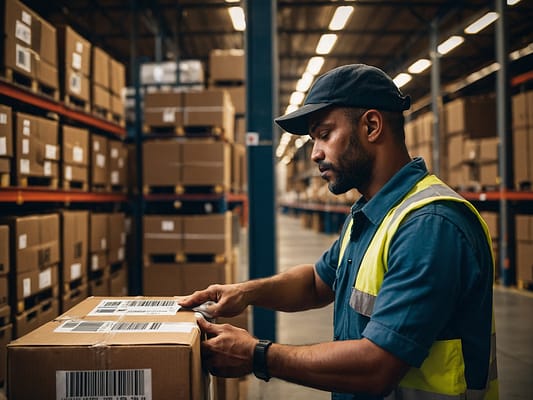
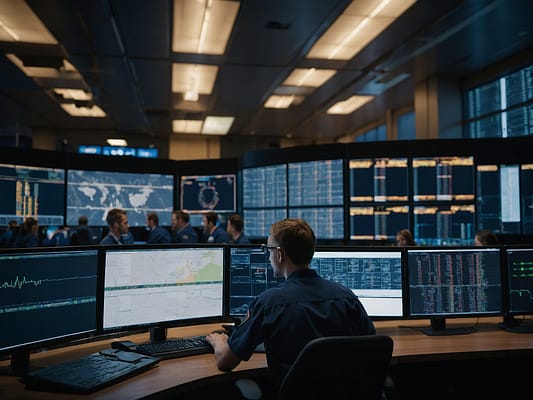
Turning a Crisis Into a Stronger System
Looking back, what could have been a logistical nightmare ended up being a valuable learning experience. We saved the shipment, reinforced our crisis management strategies, and proved that quick thinking and strong partnerships can make all the difference in logistics.
At TradeLink Solution, we know that no system is perfect, but our ability to adapt, solve problems, and learn from every challenge is what sets us apart. Logistics isn’t just about moving packages—it’s about thinking ahead, staying alert, and being ready to act when the unexpected happens.
Final Takeaway for Business Owners and Logistics Professionals
If there’s one thing this experience taught us, it’s that logistics isn’t just about moving goods—it’s about expecting the unexpected. Whether you’re managing a supply chain or running a business, always have:
🔹 A backup plan for when things go wrong
🔹 A network of reliable partners who can help in an emergency
🔹 A dedicated team monitoring critical shipments
By staying proactive, you can prevent minor shipping mishaps from turning into major disruptions.
Have You Faced a Shipping Challenge? Let’s Talk!
Have you ever dealt with a logistics nightmare that kept you on your toes? How did you solve it? Let us know in the comments or reach out to TradeLink Solution for expert logistics support.